Enhancing Quality and Efficiency: Understanding Metal Die Casting Manufacturers
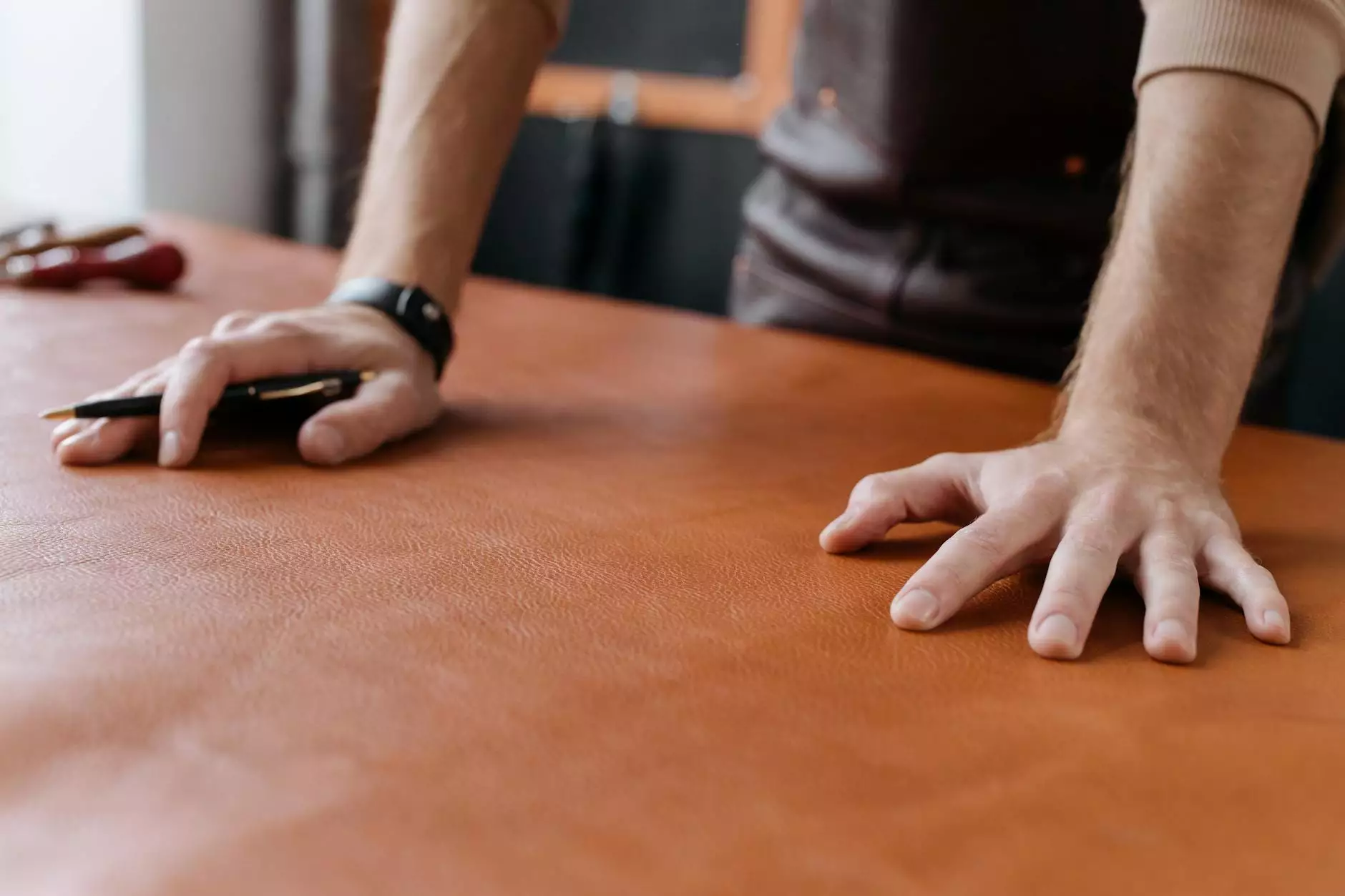
Metal die casting manufacturers play a pivotal role in modern manufacturing. As industries evolve, the demand for precision, quality, and efficiency continues to rise. This demand makes understanding the metal die casting process essential for businesses seeking to leverage high-quality components in their operations. In this comprehensive guide, we will explore various aspects of metal die casting, focusing on the manufacturers who make it all possible.
What is Metal Die Casting?
Metal die casting is a precision engineering process used to produce components by forcing molten metal into a mold. The molded components are highly detailed and can be produced in large quantities, making the process ideal for industries that require consistent and accurate parts.
Key Advantages of Metal Die Casting
- High Precision: Die casting offers remarkable dimensional accuracy, which is essential for the manufacturing of intricate designs.
- Material Variety: Manufacturers can use various metals, including aluminum, zinc, magnesium, and copper alloys.
- Efficiency: The process allows for high production rates and reduced manufacturing times.
- Cost-Effectiveness: When producing large volumes, die casting can be more economical than other manufacturing methods.
- Durability: Components produced through die casting are known for their strength and long-lasting properties.
The Die Casting Process Explained
The die casting process involves several critical steps, ensuring that each phase is executed meticulously for the best results.
1. Mold Creation
Initially, a mold is created from steel or iron, designed to the exact specifications of the desired part. These molds can be complex and are engineered to withstand immense pressure and heat.
2. Melting the Metal
The selected metal is then melted in a furnace, reaching temperatures that allow for fluidity. The type of metal chosen depends on the required properties of the final product.
3. Injection of Molten Metal
The molten metal is injected into the die under high pressure. This pressure ensures that the metal fills every crevice and cavity in the mold, resulting in a finely detailed cast.
4. Cooling and Solidifying
Once the cavity is filled, the molten metal is allowed to cool and solidify. This phase is crucial, as it affects the final integrity of the casting.
5. Ejection and Finishing
Finally, the die is opened, and the solidified casting is ejected. Additional finishing processes, such as machining or surface treatment, may be applied to enhance the final product's quality and appearance.
Applications of Metal Die Casting
Metal die casting is utilized across various industries, showcasing its versatility. Here are some notable applications:
- Aerospace: Components that require lightweight and strength, such as engine parts and structural elements.
- Automotive: Producing numerous essential parts like engine blocks, transmission cases, and structural components.
- Electronics: Manufacturing casings and housings for electronic devices that demand precision and aesthetic appeal.
- Consumer Goods: Items such as appliances and tools frequently utilize die-cast components for functionality and durability.
- Medical Equipment: Producing precise and reliable parts for devices and machinery in the healthcare sector.
Choosing the Right Metal Die Casting Manufacturer
When selecting metal die casting manufacturers, various factors must be considered to ensure you partner with a capable and reliable company.
1. Experience and Expertise
Look for manufacturers with a proven track record and significant experience in the die casting industry. Their expertise will reflect in the quality of the products you receive.
2. Quality Assurance
Quality control is paramount in die casting. Ensure that your chosen manufacturer adheres to international quality standards and employs rigorous testing methods to verify the integrity of their products.
3. Technological Capabilities
Modern die casting manufacturers utilize advanced technology and automation to enhance efficiency and precision. Assess their equipment and capabilities to ensure they can meet your needs.
4. Customization Options
Every project may have unique requirements. Choose a manufacturer that offers flexibility in design, materials, and finishing processes to accommodate specific demands.
5. Customer Support and Communication
Effective communication and customer support are vital for a successful partnership. Ensure that the manufacturer is responsive and accessible throughout the process.
The Future of Metal Die Casting
The future of metal die casting is bright, thanks to ongoing advancements in technology and materials. Here are some trends that are shaping the industry:
- Increased Automation: Automation in die casting processes leads to higher efficiency, reduced lead times, and more consistent quality.
- Lightweight Materials: As industries like automotive push for lighter components, manufacturers are exploring new alloys that provide strength without added weight.
- Sustainability Efforts: Manufacturers are increasingly adopting sustainable practices, including recycling metals and reducing waste during the casting process.
- Enhanced Simulation Software: Advanced simulation tools allow manufacturers to optimize designs and casting processes before the actual manufacturing begins, reducing errors.
- Expanded Industry Applications: As technology progresses, more industries are likely to discover innovative uses for die-cast components.
Conclusion
In summary, metal die casting manufacturers hold a crucial place in the manufacturing landscape. Their role in providing high-quality, durable parts is indispensable for various industries. Understanding the die casting process, recognizing its advantages, and selecting the right manufacturer can empower businesses to enhance their products and achieve greater efficiency. As technology continues to evolve, the potential for die casting will expand, paving the way for even more innovative applications in the future.
For the highest quality components through a dedicated and expert team, consider Deep Mould, where precision meets experience in the world of metal die casting.