Understanding Pressure Die Casting Components: A Comprehensive Guide
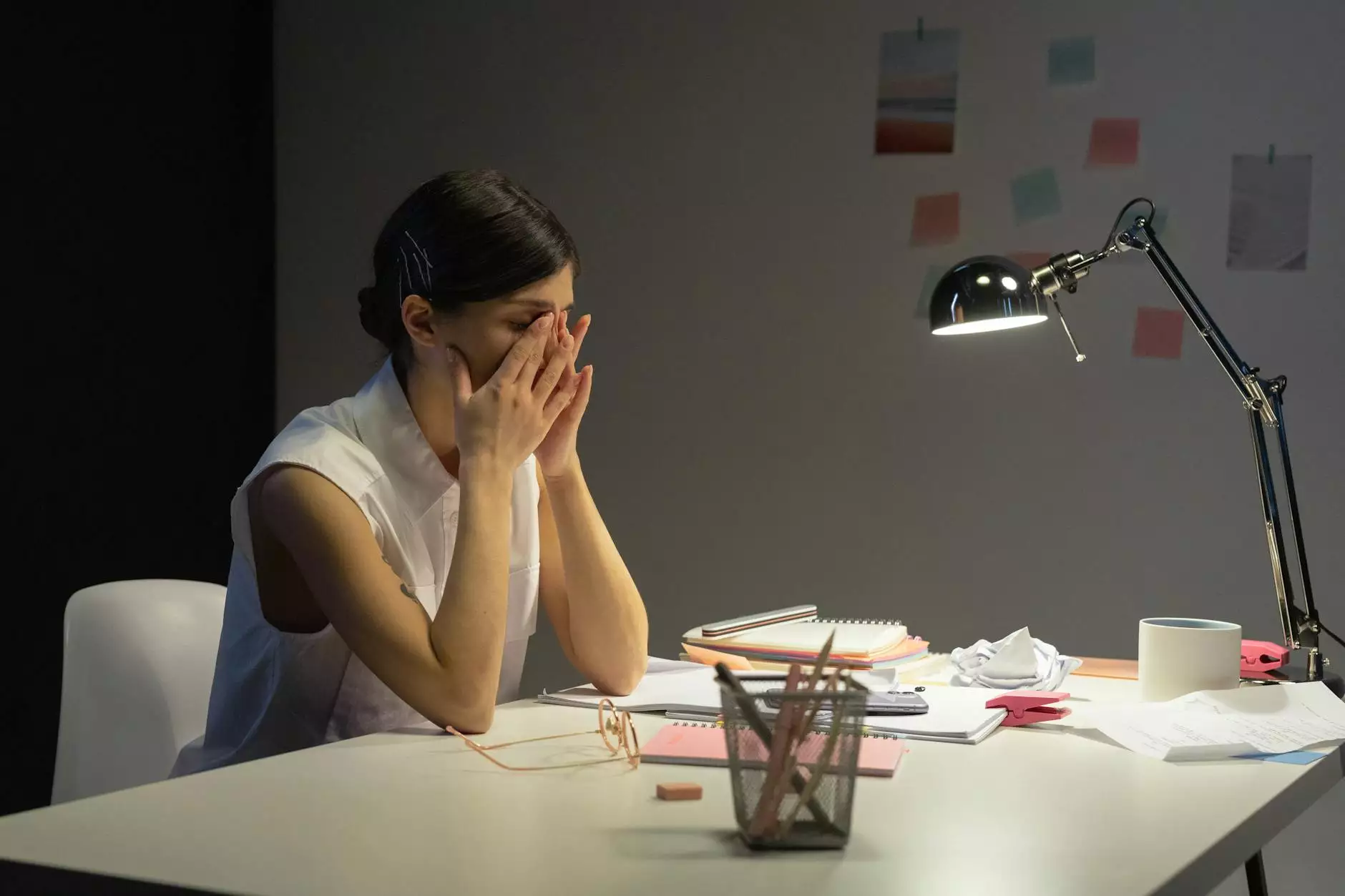
Pressure die casting is a manufacturing process commonly used to produce parts for various industries. It is particularly prominent in the production of metal components due to its efficiency and precision. In this article, we will explore the intricate details surrounding pressure die casting components, their benefits, manufacturing processes, applications, and what the future holds for this essential business sector.
What are Pressure Die Casting Components?
Pressure die casting components are metal parts created by forcing molten metal into a mold under high pressure. This technique allows for the production of complex shapes with an excellent surface finish and precise dimensions. The primary metals used in this process are aluminum, zinc, and magnesium, each chosen for their unique properties and suitability for specific applications.
History of Pressure Die Casting
The origins of die casting can be traced back to the late 19th century. The process has evolved significantly from its manual beginnings to modern automated systems that boast high output and repeatable quality. The advent of pressure die casting revolutionized the manufacturing process, allowing for faster production times and more complex designs, which led to improved product performance across numerous applications.
The Process of Pressure Die Casting
Understanding the process involved in creating pressure die casting components is crucial for appreciating their value. Here’s a step-by-step breakdown:
1. Mold Design
The first step involves designing the molds, which are typically made from hardened steel to withstand high pressure and temperature. Mold designs must account for thermal expansion and contraction as well as proper drainage for excess material.
2. Melting the Metal
The selected metal is heated in a furnace until it reaches a molten state. The temperature and composition must be carefully monitored to ensure optimal flow and strength properties.
3. Injection of Molten Metal
Once the metal is molten, it is injected into the mold at high pressure using a piston or plunger system. This ensures that the metal fills every aspect of the mold, capturing intricate details and reducing the chance of defects.
4. Cooling and Solidification
The molten metal is left to cool and solidify, which usually takes a matter of seconds to minutes depending on the complexity of the part. Cooling rates can affect the mechanical properties of the final product.
5. Ejection and Finishing
After solidification, the mold opens, and the finished component is ejected. This stage may include additional finishing processes such as machining, polishing, or surface treatment to meet specific requirements.
Advantages of Pressure Die Casting
There are several advantages of using pressure die casting components that make this method a favored choice among manufacturers:
- High Precision: The use of high-pressure injection ensures that the components produced are highly accurate in dimensions.
- Quality Surface Finish: Parts produced through this method typically require less machining and finishing.
- Complex Geometries: Pressure die casting allows for intricate designs that might be unachievable through other manufacturing processes.
- Material Efficiency: Minimal waste is generated during the casting process, making it environmentally friendly compared to other methods.
- Rapid Production: High-speed cycle times allow for large quantities of parts to be produced quickly.
Common Applications of Pressure Die Casting Components
The versatility of pressure die casting components has led to their widespread adoption across various industries, including:
1. Automotive Industry
Many components, such as engine blocks, transmission cases, and decorative parts, are manufactured using pressure die casting due to the strength and lightweight nature of the cast metals.
2. Electronics
Enclosures and heat sinks for electronic devices are often made from aluminum die castings, providing thermal management and structural integrity.
3. Aerospace
For aerospace applications, where weight reduction is critical, pressure die casting components provide the necessary strength-to-weight ratio required for various parts.
4. Consumer Goods
From small household appliances to fittings, pressure die casting components can be found in everyday consumer products where durability and design are essential.
Future Trends in Pressure Die Casting
The future of pressure die casting components looks promising, with several trends shaping the industry:
- Automation and Industry 4.0: The integration of smart technologies and automated processes is enhancing production efficiency and quality control.
- Advanced Materials: Continued research into new alloys and materials will lead to even better performance of die cast components in demanding applications.
- Sustainability Efforts: As companies focus on reducing their environmental footprint, pressure die casting processes are being evaluated for energy efficiency and sustainability.
- Enhanced Software Technology: The utilization of simulation software in the design phase of die casting will further improve the accuracy and efficiency of manufacturing processes.
Conclusion
In conclusion, pressure die casting components are integral to many industries due to their cost-effectiveness, precision, and versatility. As technology evolves, the capabilities of pressure die casting continue to expand, making it an essential part of modern manufacturing. Companies looking to optimize their production capabilities must consider the advantages that pressure die casting offers and explore innovative solutions to stay competitive in their respective markets.
For businesses interested in leveraging the benefits of pressure die casting, partnering with experienced manufacturers such as Deep Mould can provide the expertise needed to ensure top-quality components that meet stringent industry standards.