Maximizing Efficiency and Reliability with PLC Repairs
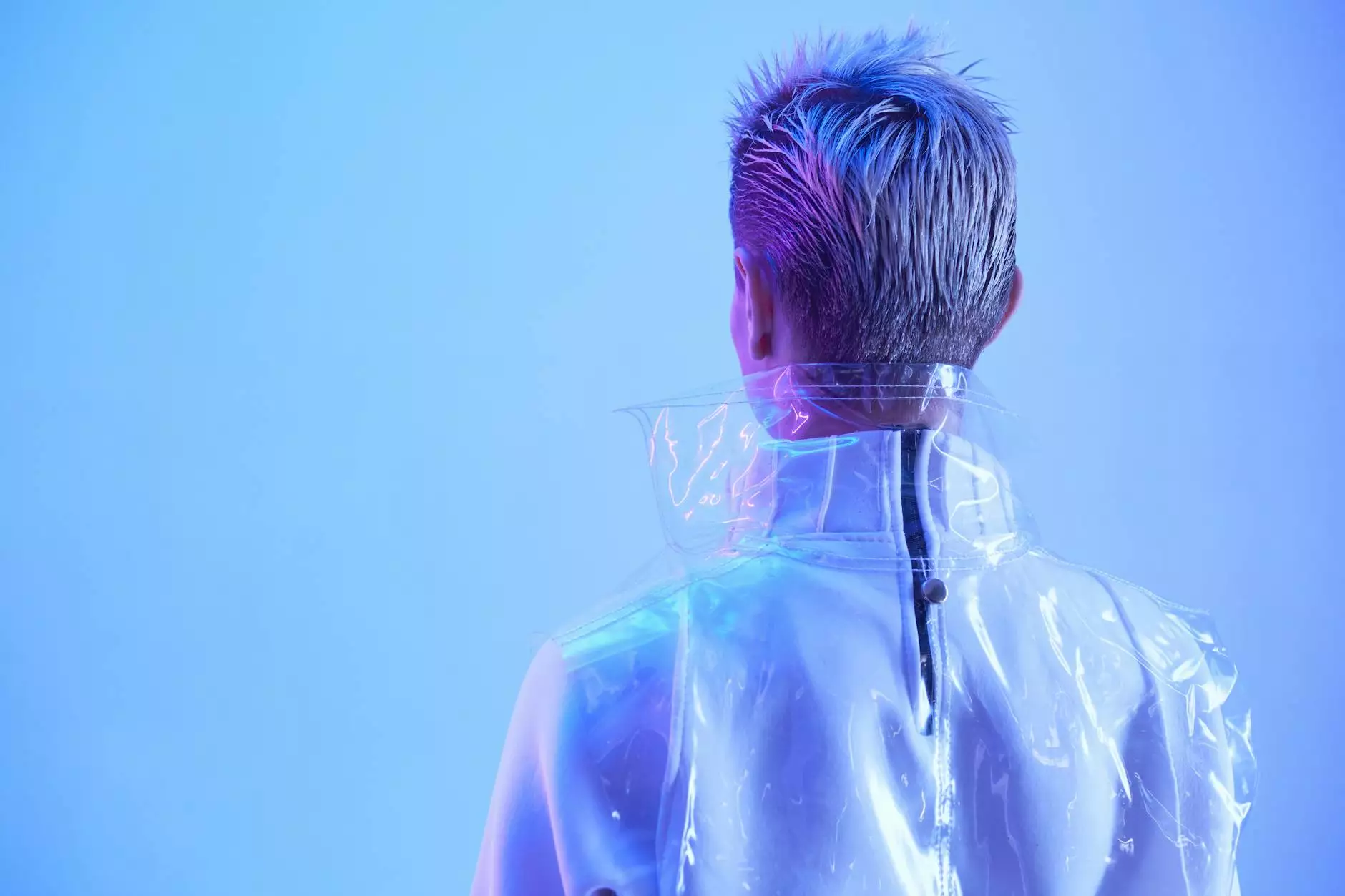
In the fast-paced world of industrial automation, Programmable Logic Controllers (PLCs) stand as the backbone of operational efficiency. As businesses strive for seamless productivity and reliability in their processes, the demand for effective PLC repair services cannot be overstated. This article delves into the critical role that PLC repairs play, particularly in the context of electronic components distribution in Canada, and highlights how QF Automation can deliver unmatched expertise and service quality.
The Importance of PLCs in Modern Business
PLCs are vital for managing automation equipment and processes in various industries, including manufacturing, food processing, and material handling. Their ability to control machinery and process flows makes them indispensable. However, like any technology, they are prone to failures and require proper maintenance and repairs. Understanding the significance of PLCs is crucial for businesses aiming to maximize efficiency and minimize downtime.
Understanding Common PLC Issues
While PLCs are designed for robustness, they can develop issues due to various factors, including:
- Electrical Surges: Unexpected power spikes can damage the internal circuitry.
- Heat: Overheating can lead to component failure, especially in high-demand situations.
- Moisture: Exposure to humidity can corrode connections and internal circuits.
- Wear and Tear: Continuous operation may lead to mechanical failures over time.
How PLC Repairs Enhance Business Continuity
Properly functioning PLCs ensure that industrial processes run smoothly. However, when a PLC malfunctions, it can halt operations, leading to substantial financial losses. This is where expert PLC repairs become essential. The timely intervention of trained professionals can rectify issues, ensuring minimal downtime and restoring operational efficiency. Here’s how PLC repairs enhance business continuity:
1. Minimizing Downtime
Every minute a manufacturing line is down translates to lost revenue. Skilled PLC repair technicians can diagnose issues quickly, performing repairs in a timely manner that reduces overall downtime, allowing businesses to maintain production schedules and meet customer demands.
2. Extending Equipment Lifespan
Regular maintenance and prompt repairs can significantly extend the lifespan of automation equipment. By addressing problems early, businesses can prevent catastrophic failures that would lead to costly replacements.
3. Enhancing Safety
Faulty PLCs may lead to unsafe operating conditions. Effective repairs not only restore functionality but also ensure that safety protocols remain intact, protecting employees and equipment alike.
Choosing the Right PLC Repair Service
Selecting a reliable PLC repair service is crucial for achieving the above benefits. Here are some key factors to consider:
- Expertise: Look for technicians with thorough knowledge of various PLC brands and models.
- Rapid Response: Choose a service that can respond quickly to urgent repair needs.
- Quality Assurance: Ensure that the service provider has a robust quality control process to guarantee effective repairs.
- Customer Support: Evaluate the level of ongoing support available, including post-repair assistance.
QF Automation: Your Premier PLC Repair Partner
At QF Automation, we understand that your business operations depend on the reliability of your PLC systems. Our team is dedicated to providing high-quality PLC repair services across Canada. Here’s what sets us apart:
Unmatched Technical Expertise
We employ highly qualified technicians with extensive experience in troubleshooting and repairing various PLC models. Our team stays updated with the latest technologies and methodologies to ensure that we deliver top-notch service for every client.
Comprehensive Service Offerings
QF Automation offers a range of services that not only cover PLC repairs but also include component distribution and system upgrades. This comprehensive approach allows our clients to receive unified services tailored to their unique needs.
Rapid Turnaround Times
We recognize that time is of the essence in industrial operations. Our streamlined repair process and effective diagnostics ensure that we minimize turnaround times, helping your business to resume operations quickly.
Client-Centric Approach
Your satisfaction is our priority. We work closely with our clients to understand their specific requirements and challenges, providing customized solutions that align with their business goals.
Investing in Preventative Maintenance
Prevention is always better than cure. To further protect your investment in PLC technology, consider implementing a preventative maintenance program. This proactive approach ensures that any potential issues are identified and addressed before they escalate into significant problems. Here are the key components of an effective preventative maintenance program:
Routine Inspections
Schedule regular inspections to assess the health of your PLC systems. Early detection of wear and tear can save you from costly breakdowns.
Firmware Updates
Keep your PLCs updated with the latest firmware. This not only enhances functionality but also improves security against vulnerabilities.
Training for Staff
Equip your team with knowledge about basic PLC functions and troubleshooting techniques. Empowering your staff can lead to quicker responses to minor issues, reducing the likelihood of major failures.
The Future of PLC Technology and Repairs
The automation industry is continuously evolving with advancements in technology. The emergence of Industry 4.0, artificial intelligence, and IoT (Internet of Things) is reshaping how PLCs operate. As more businesses adopt these technologies, it is essential that PLC repair services also adapt to meet new challenges and requirements. Consider these trends:
Integration with IoT
PLCs are increasingly being integrated with IoT devices, providing real-time data and analytics. This integration not only enhances operational efficiency but also presents new challenges for maintenance and repair, making specialized knowledge invaluable.
Predictive Maintenance
With advancements in analytics, businesses are moving towards predictive maintenance models that utilize data trends to forecast equipment failures before they occur. This proactive strategy can significantly mitigate repair costs.
Conclusion
In conclusion, investing in expert PLC repairs and prioritizing preventative maintenance is essential for businesses seeking to maintain operational continuity and drive profitability. With the support of QF Automation, your business can navigate the complexities of PLC operations with confidence. Our dedicated team stands ready to enhance your automation systems and ensure your processes remain efficient and reliable.
Contact QF Automation today to learn how our PLC repair services can revolutionize your business operations.